Whoa! Hold it down out there!
- Phil Barrett
- Feb 20, 2022
- 2 min read
Updated: Aug 31, 2022
Keeping your workpiece from moving is gospel to CNCers and there are a million ways to do it. There seems to be no end of commercial hold-downs and clamps for CNC routing. Some are amazingly expensive. They may be clever and well engineered but to me they are all just consumables. I make my own out scrap stock and don't cry when I slice through one. I think it is a rare CNCer that hasn't hit more than a couple of clamps.
Before I show you my approach, what are the characteristics of good a hold-down?
First and foremost, it must be able to apply enough pressure to prevent the workpiece from moving.
Does not interfere with movement of the spindle or collet/nut.
Does not require contact to a lot of the workpiece to work well. This is to minimize waste.
Is sacrificial - if the bit hits it, the bit should survive.
Is very inexpensive and quick to make.
As you can see in the photo below, my clamps are simple. They consist of the clamp arm, a knob, a T-nut and 1/4-20 hex headed bolt. In some cases I also use a 1/4" washer. The clamp arm has a 1/8" x 1/8" rabbet in the end that allows me minimize the actual clamping area needed on the workpiece. Total cost for one clamp, using McMaster-Carr prices, is $0.20-0.35 depending on how long the 1/4-20 bolt is. Of course, you can find cheaper prices and may just have a few spare lying around in your shop. Since I used scrap wood for the knobs and arms, I price that at 0 because I would have otherwise tossed it out.

I designed my spoil board to incorporate T-Track that accepts 1/4-20 hex head bolts. The T-Track was purchased from Orange Aluminum and was surprisingly inexpensive. It didn't have screw holes but I didn't mind drilling them in order to save more than a hundred bucks. The clamps are easy to position along the track. I use different length bolts depending on the height of the workpiece. Below is an example of how I use them.


I make the clamp arms out of 1/2"/12mm plywood and the knobs out of 3/4"/18mm plywood. My clamp arms are 4" and 5" long. I have found 4" is just a little short with my T-Track spacing. Routing time for a batch of 6 with a 1/4" bit is around 4 minutes so it is pretty fast to make them. I tried making round knobs but found that the style I use allows me to turn them so they are away from the cutting area and do not interfere with the spindle. You can always add a quarter turn after it is tight. This allows me to clamp right up to the cut line even with a really short bit in my ER25 collet. In addition, the two arms give me more leverage when tightening.
Here are the dimensions of the wooden parts.

.
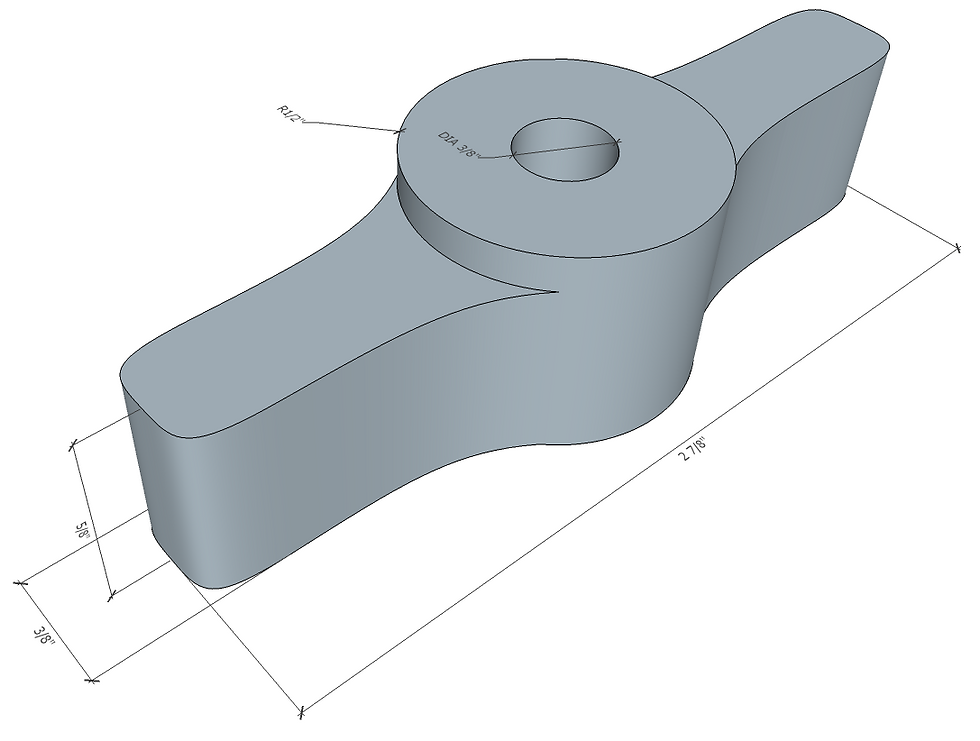
About Me
I'm a CNC enthusiast. I run a small company, Brookwood Design, that makes a 32-bit Grbl breakout board for grblHAL and love to help people get the most out of their CNC machines.
Recent Posts
See AllMultiple times a day, people ask for help with their CNC machine. Many supply enough detail for the experts in the group to give good...
This style of clamp works better if the rear of the clamp is higher than the front. Use some scrap pieces under the tail. This is because a clamp that slopes up towards the workpiece applies a sideways force as well as a downwards one. If the workpiece gets pushed in that direction it can move quite easily.