Dustin' up!
- Phil Barrett
- Oct 20, 2021
- 5 min read
Updated: Sep 10, 2023
Or perhaps down. Dust collection is a topic of much interest in the CNC world. Nothing is more annoying than getting everything covered in CNC dust. And, more importantly, dust in the air is a hazardous substance. This is especially true for those with lung disease or other medial issues that affect breathing. Here is a tour of my dust collection system. My goals were pretty simple - collect the dust and swarf from the work area, avoid making tool changes hard, filter down to 1 micron particle size (for lung health) and capture most of the dust before it enters the main dust collector to maximize filter life.
I have built several dust collection systems in the past.: a moderate sized one for my shop based on a 1 HP Grizzly dust collector, A small one based on a small shop vac for my CBeam CNC router and a mobile cart for sanders and saws based on a medium sized shop vac with a HEPA filter. All of them have a cyclonic separator to reduce load on the filter. These use a Thein Baffle that catches most of the dust before it gets to the vacuum/collector. I will do a blog entry on the Thein Baffle at some point.
For the Avid Pro4848, I decided to have a dedicated dust collector and settled on the Grizzly G0944 1.5 HP wall mounted unit with a canister based 1 micron filter. You can see it in the photo below. It has 1250 CFM (cubic feet per minute) and a reasonable price of $625. I definitely wanted a spec'd CFM of greater than 1000. If you do much research you will find that CFM ratings in general are kind of wishful thinking. You will only get that with the collector not actually connected to anything. Every bit of piping drops the actual number. Sigh. My theory in this case is bigger is better. Did the G0944 meet the goals? Read on!

I also decided to use 4" PVC pipes to hard plumb it as much as possible - the flexible 4" piping you see in a lot of collection systems really decreases airflow and robs you of precious CFM. Every elbow connection does too. As does every little ridge or what ever. So Keeping the number of turns to a minimum was important. As you can see I wound up with 4 90 degree turns. I could have avoided one if I was able to place the collector farther to the right but that would have entailed either moving the light fixture or going under it. Neither of which was desirable. Some of you are saying "well you could have just left off that black one and connected the flex hose. Yes, I could have but a flex hose 90 degree turn is a worse CFM killer than a PVC one.

The photo shows my complete system and the key components: collector, separator, plumbing, dust shoe and riser. I discussed the collector already so on to the dust shoe. I designed the dust shoe myself. I've made several before and had a pretty good sense of what I wanted. The key is that it has to provide enough airflow to pull the dust, chips, swarf, whatever into the flex hose and eventually to the separator. But it also has to allow easy tool changes. To that end, I designed it to be in 2 parts - a removable brush and clamping bracket. The clamping bracket uses a toggle clamp to hold it to the spindle. The toggle clamp allows me to adjust the height on the spindle to accommodate different length router bits. It works pretty well but if I did it over again, I would use stronger magnets.
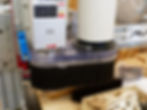
The clamping bracket also has a port to connect the flex hose to. The brush connects to the clamping bracket via magnets so it is easy to take off or put on. One thing I did with my other CNC machine was to set it up so the dust collector could be used for general machine clean up. That turned out to be super useful so I didn't use a pipe clamp to permanently connect the port to the flex hose but rather used the Rockler Dust Right quick connect fitting. This allows me to pull it off the dust shoe and connect a nozzle for general clean up. I like to keep my work area dust free.

Here you can see the clamping bracket pulled off the spindle, along with the Dust Right quick connect fitting and the desktop nozzle. So far I am very happy with this set up - it works exactly the way I wanted.
On to the dust separator. You can buy commercial separators like the dust deputy and others but I prefer to build my own using Phil Thein's baffle. It is easy to build and you can buy kits that make it even easier. I decided to try something a little different - a top hat design that I had been thinking about for years.
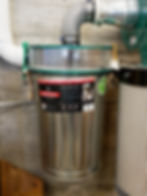
Here you can see the general design of the separator. The key is the curved slot in the bottom plate which is called a Thein Baffle after the inventor, Phil Thein. The collector is connected to the top dust port and pulls the dust in from the side port. The side entry forces the air into a cyclone which slows the flow and allows most of the dust to drop out through the curved slot and into the trash can below. The remaining dust is pulled through the top port into the collector which is filtered out in the canister filter. The curved polycarbonate (AKA Lexan) window makes it easy to see how well it is working. As you can see in the drawing below, it is a perfect project for a CNC machine!

The sharp eyed reader will notice that the trash can is not completely pressed against the bottom of the separator. This is not a problem because when the collector is turned on, the resulting vacuum pulls the trash can firmly against the bottom. Foam weather stripping on the bottom of the separator ensures a fairly air tight connection. I am happy to say that it seems to work better than I had hoped. After a couple of hours of use, there is almost no dust in the plastic bag under the G0944 and about 5 inches in the trash can under the separator. It is a bit early and some of the dust that didn't go into the separator is in the filter itself. Once the filter loads up a bit more, I will run a test to see just how effective the separator is but I think it gets around 90% of the dust.
So there you have it.
And, to the question at the beginning of the this blog - does the Grizzly G0944 dust collector work well? The answer is yes. I get good air flow at the dust shoe and it collects almost all the dust, chips and swarf. My biggest complaint is that it doesn't have a hard wired switch. I also want to be able to start and stop the collector at the same time as the spindle. I've looked into hacking the starter box - it's doable. Also, the machine is turned on/off with a remote switch fob that feels very flimsy. If it dies, there is no way to turn the machine on or off. About Me.
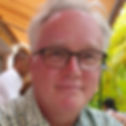
I'm Phil Barrett, a long time CNC enthusiast. I run a small company, Brookwood Design, that makes several breakout boards for grblHAL and love to help people get the most out of their CNC machines.
Recent Posts
See AllMultiple times a day, people ask for help with their CNC machine. Many supply enough detail for the experts in the group to give good...